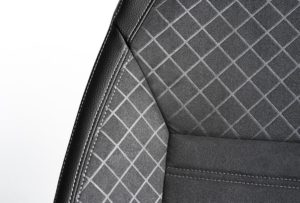
As the premier provider of engineered materials solutions and flexible multi-layer materials for automotive interiors, we create a wide range of automotive material solutions — from sun visors and automotive headliner fabric to door and console trims, overhead sunshades, and automotive seating fabrics.
With a range of fabric lamination and advanced textiles manufacturing services that are unmatched across the market, we are dedicated to customer collaboration and custom solutions capabilities to bring unrivaled value to our customers.
With premium-look fabrics like Neoluxe™, we create a design journey to tell your product’s story.
Our vertical integration from fabric design, through engineering, knitting, dyeing, finishing, testing, and lamination ensures well-managed and targeted results.
Discover how Shawmut’s spacer knit fabric revolutionized automotive interior door bolsters with comfort, durability, and sustainability.
InfinKnit™ Spacer Knit represents a groundbreaking advancement in automotive interior materials, offering a revolutionary alternative to traditional foam-based solutions and face fabrics.
How can we help you solve your most pressing automotive materials challenge?
Get inspired by these material innovations.
Neoluxe™ captures the luxurious surface of suede with the consistency and trimmability of a knit. It serves as a sustainable option to urethane-impregnated non-woven microfiber materials, crafted from homogenous materials with a lower carbon footprint.
Designed for a wide range of automotive interior applications—seating, headliners, visors, shades, pillars, doors, and more—Neoluxe integrates seamlessly into 100% PES composites, ensuring recyclability without the need for TPU impregnation.
Soft, inviting, rich in color, and visually striking, Neoluxe delivers an exquisite experience.
Click here to see more.
Heather fabrics create subtle textures that provide a soft, comforting atmosphere to any automotive interior.
They have a composite structure that creates a stunning two-tone appearance. Heather comes in a multitude of shades and subtle textures.
Inspired by home interior textiles, our line of Heather materials provide a soft, relaxing environment. Heather is available in multiple shades and knit structures to design for the perfect fit through carefully crafted yarns and subtle texture.
Click here for more.
At Shawmut, we strive to produce sophisticated materials with dimension and durability. Our Terra fabrics not only embody elegance but are sustainably produced.
Terra innovates with reduced impact on our planet.
Our recycled-content materials dramatically reduce:
• Water consumption
• Natural gas/other energy consumption
• Dyes and chemical usage
• Raw materials from petroleum chemicals
• Burden on natural resources
Click here for more.